maximize your production
The easy-to-use skills management and assignment planning software,
modern and efficient for production teams.
Book a demo
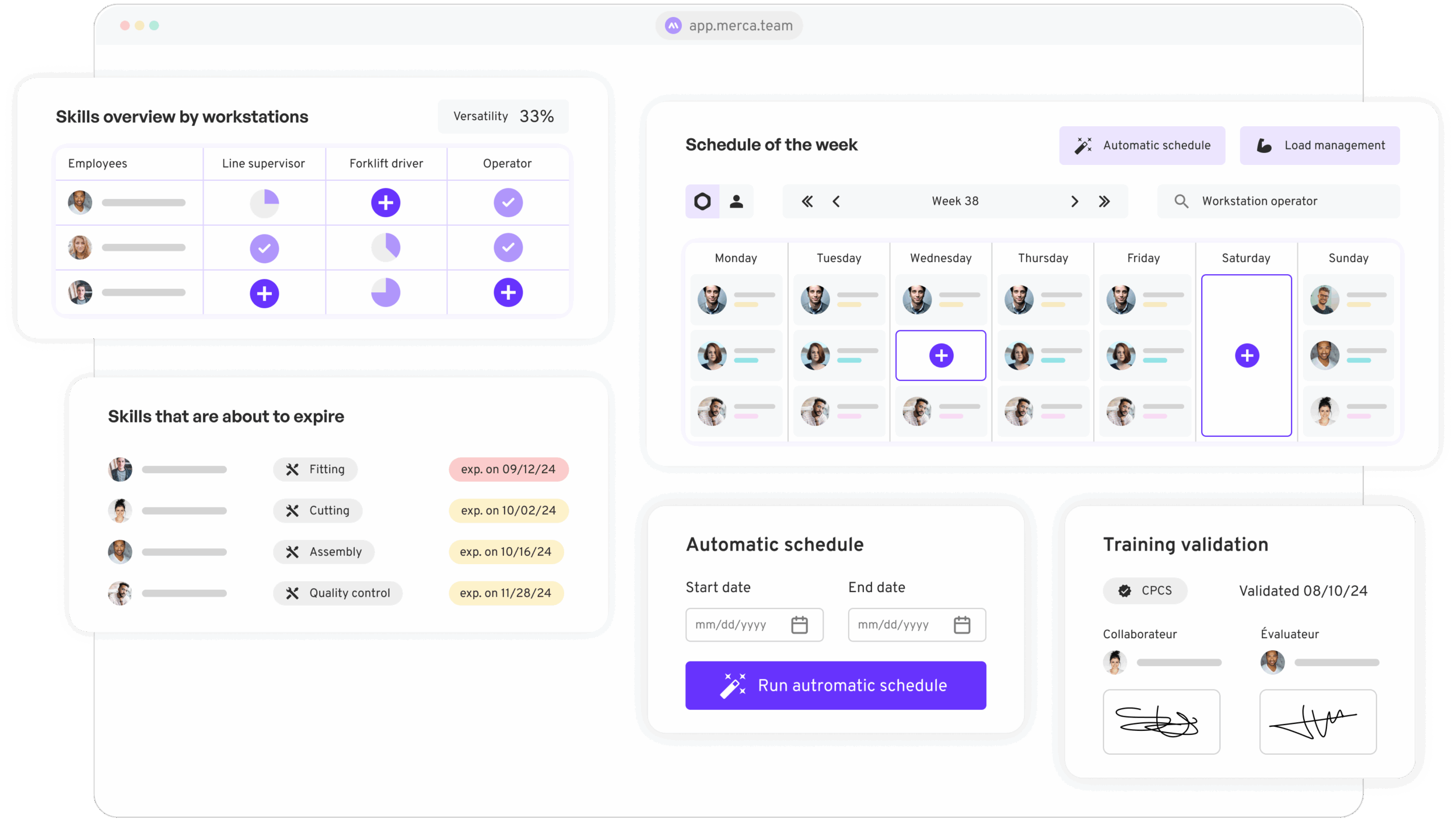
A centralized platform that puts people back at the heart of Industry 4.0.
SKILLS MATRIX
Keep your frontline workers’ skills always up to date

ASSIGNMENT SCHEDULE
Create compliant shift schedules in just a few minutes
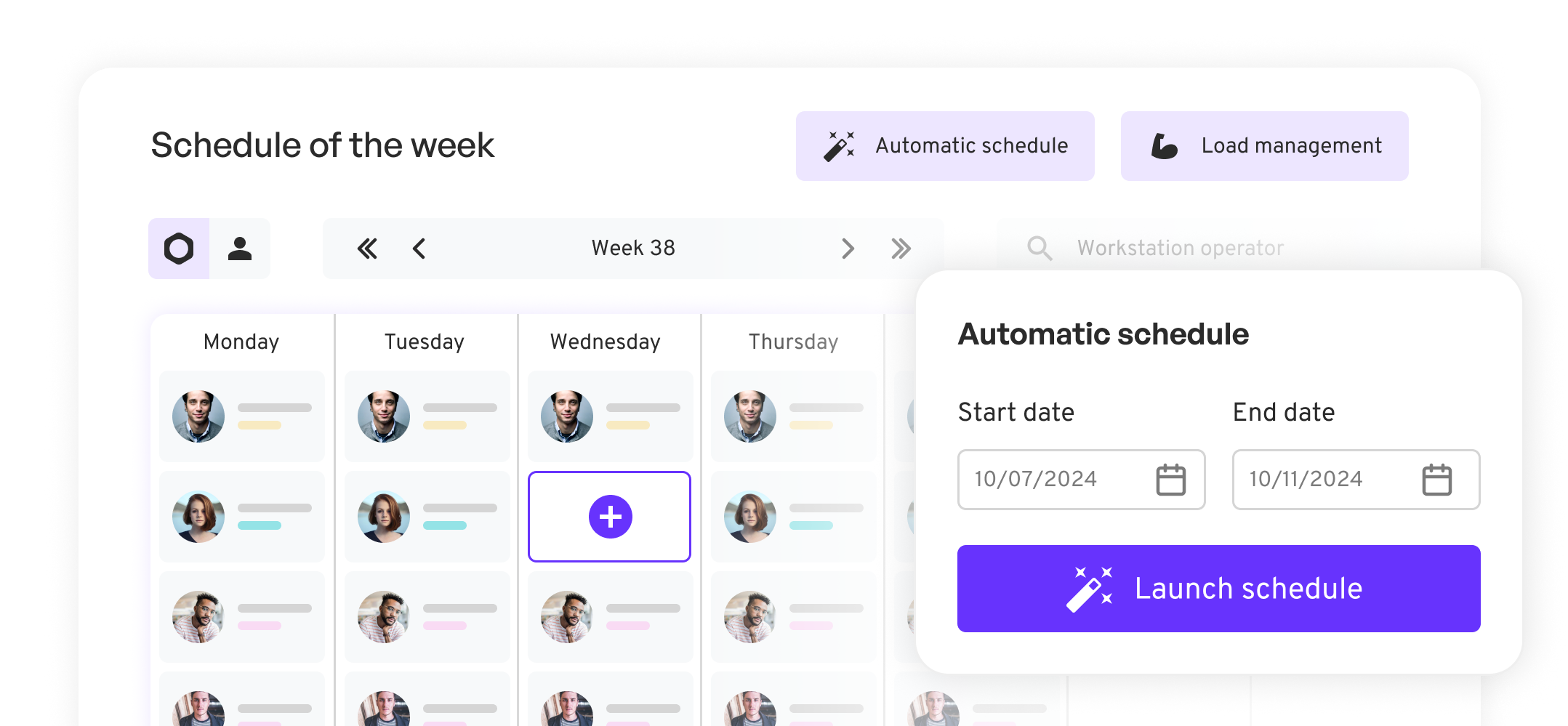
TRAINING
Production teams more versatile than ever

FIELD DATA
Field data to manage your operations
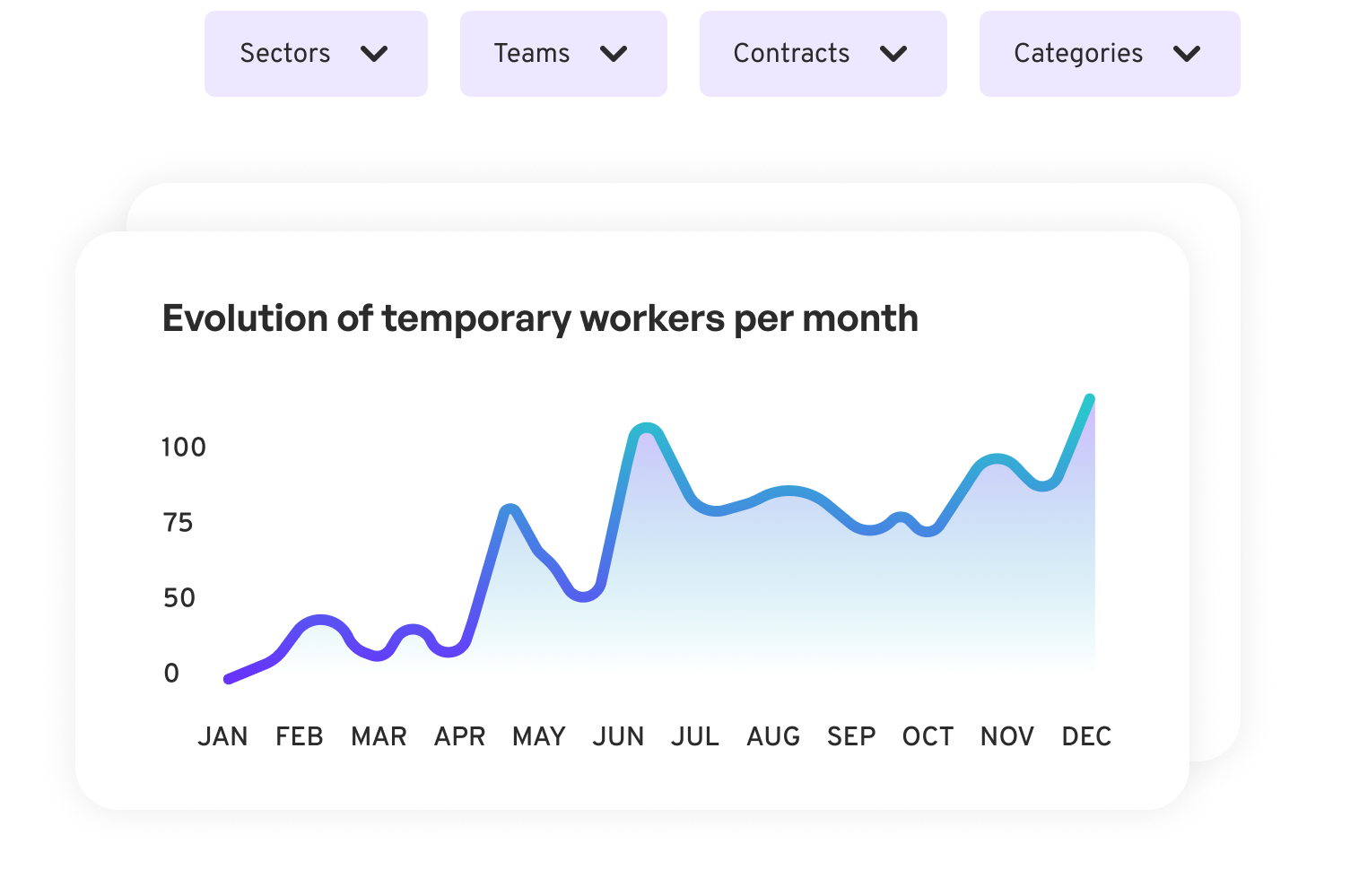
WORK INSTRUCTIONS
The shopfloor know-howat your fingertips
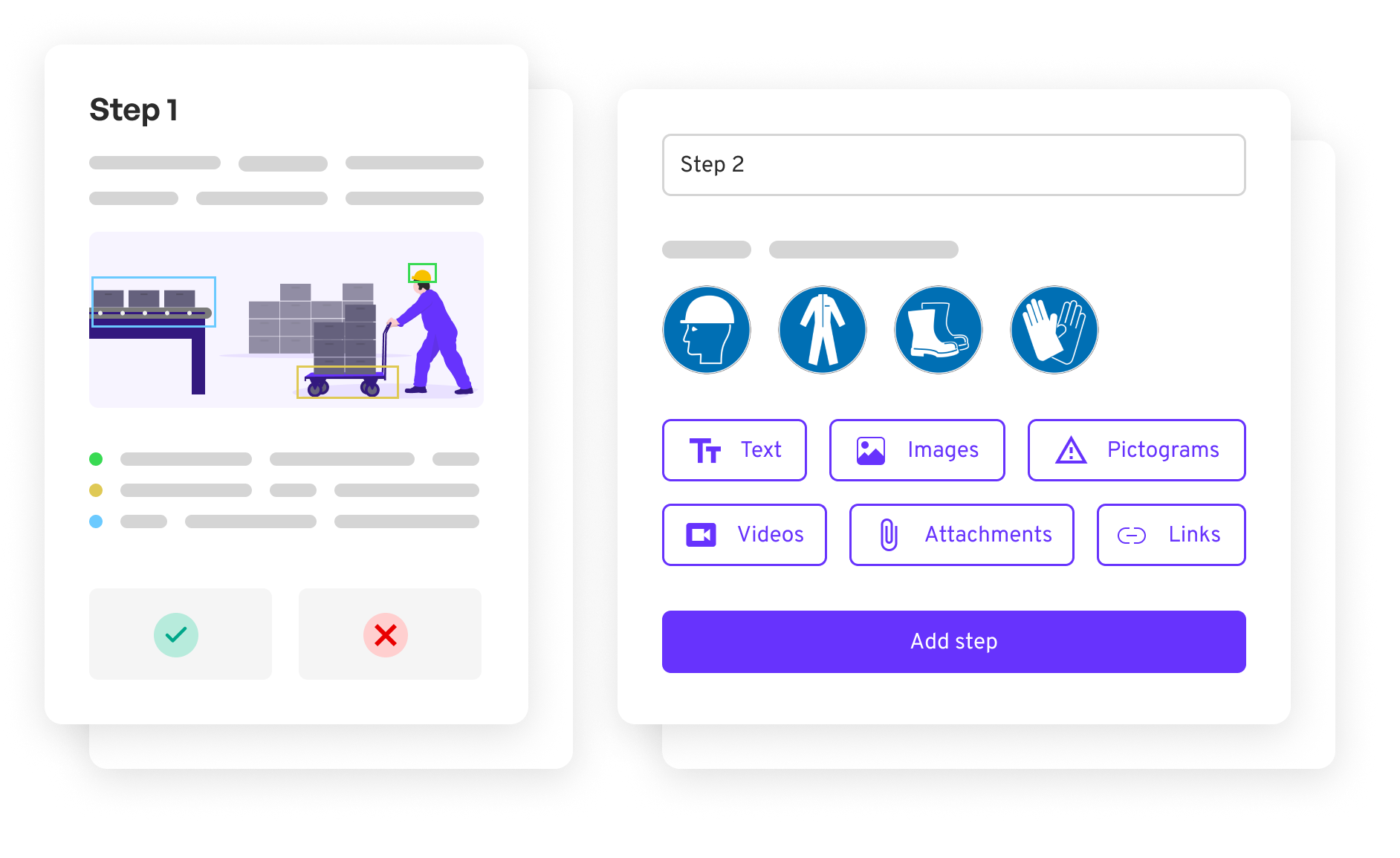
The real value our customers
unlock every day with Mercateam
Reliability
Time
Agility
ERP and HRIS
integration
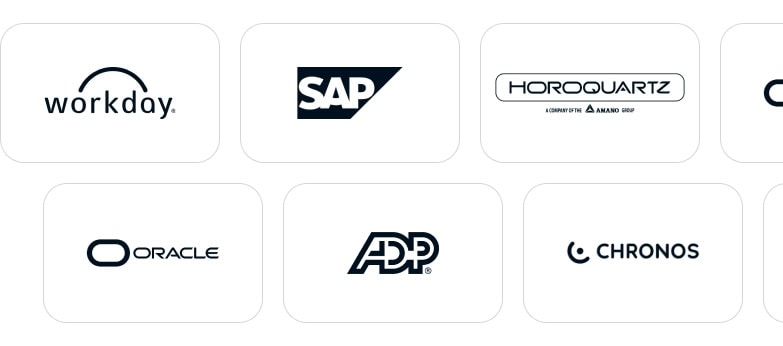
Customized support to make your project a success

Florent Bonne
Production Manager, SKF
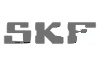
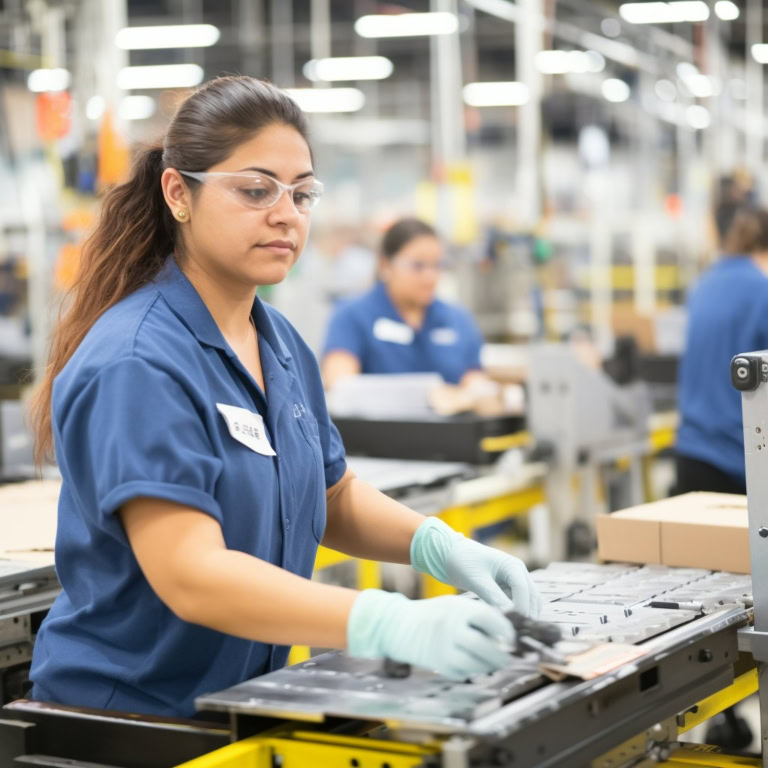
- Cosmetics
- Pharmaceuticals
- Food industry
- Aeronautics
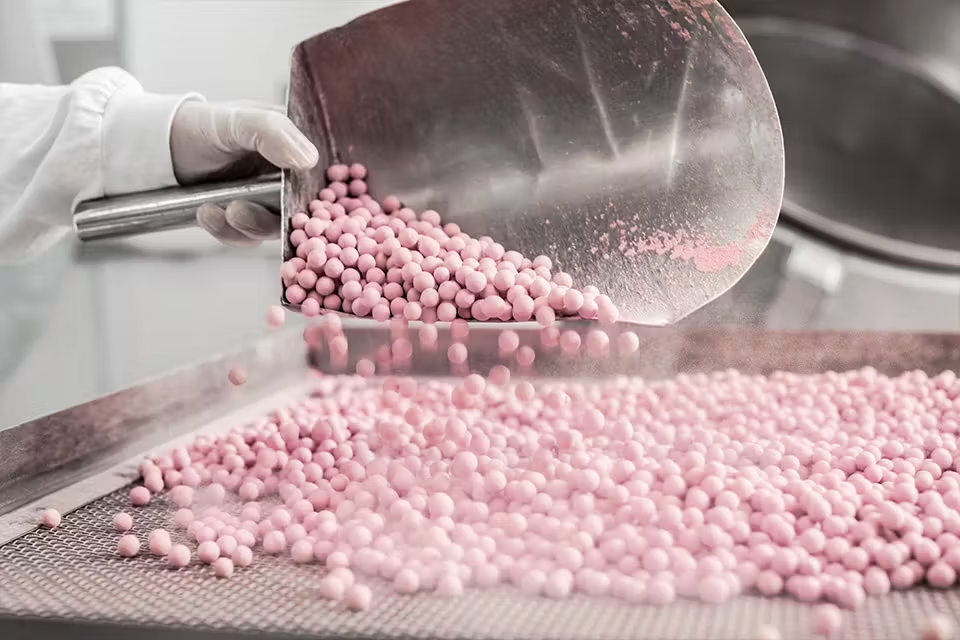
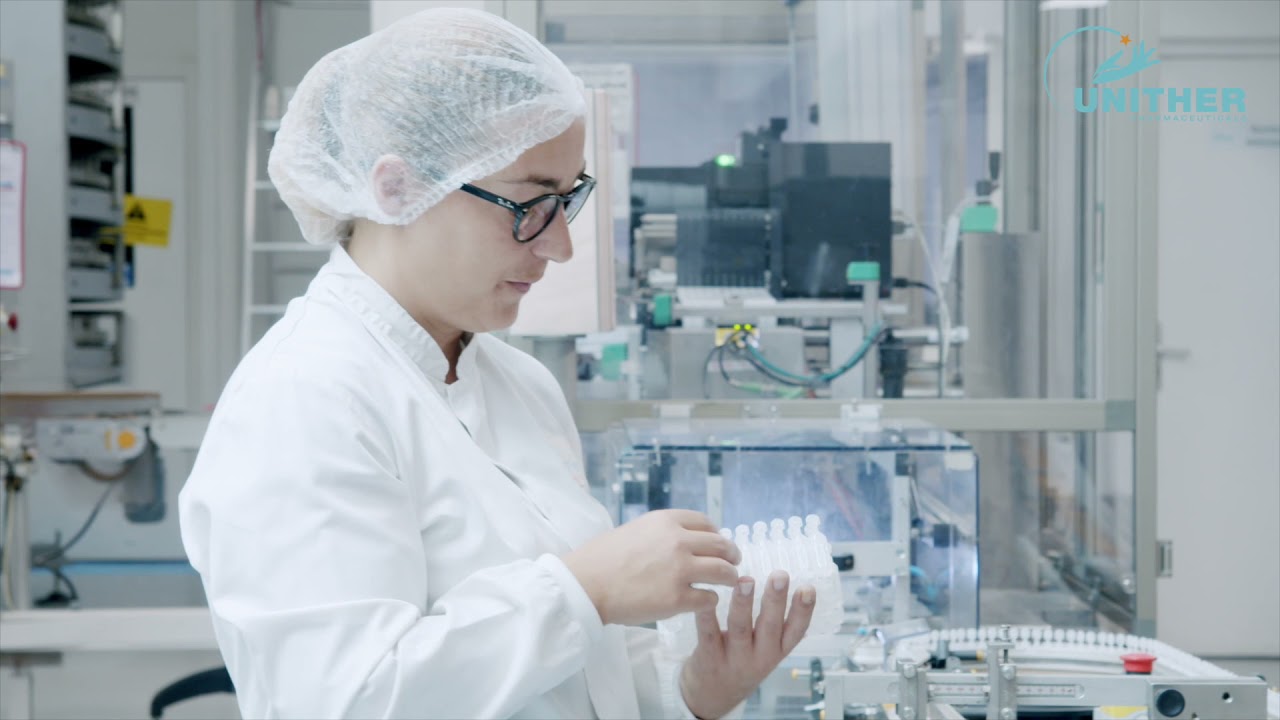
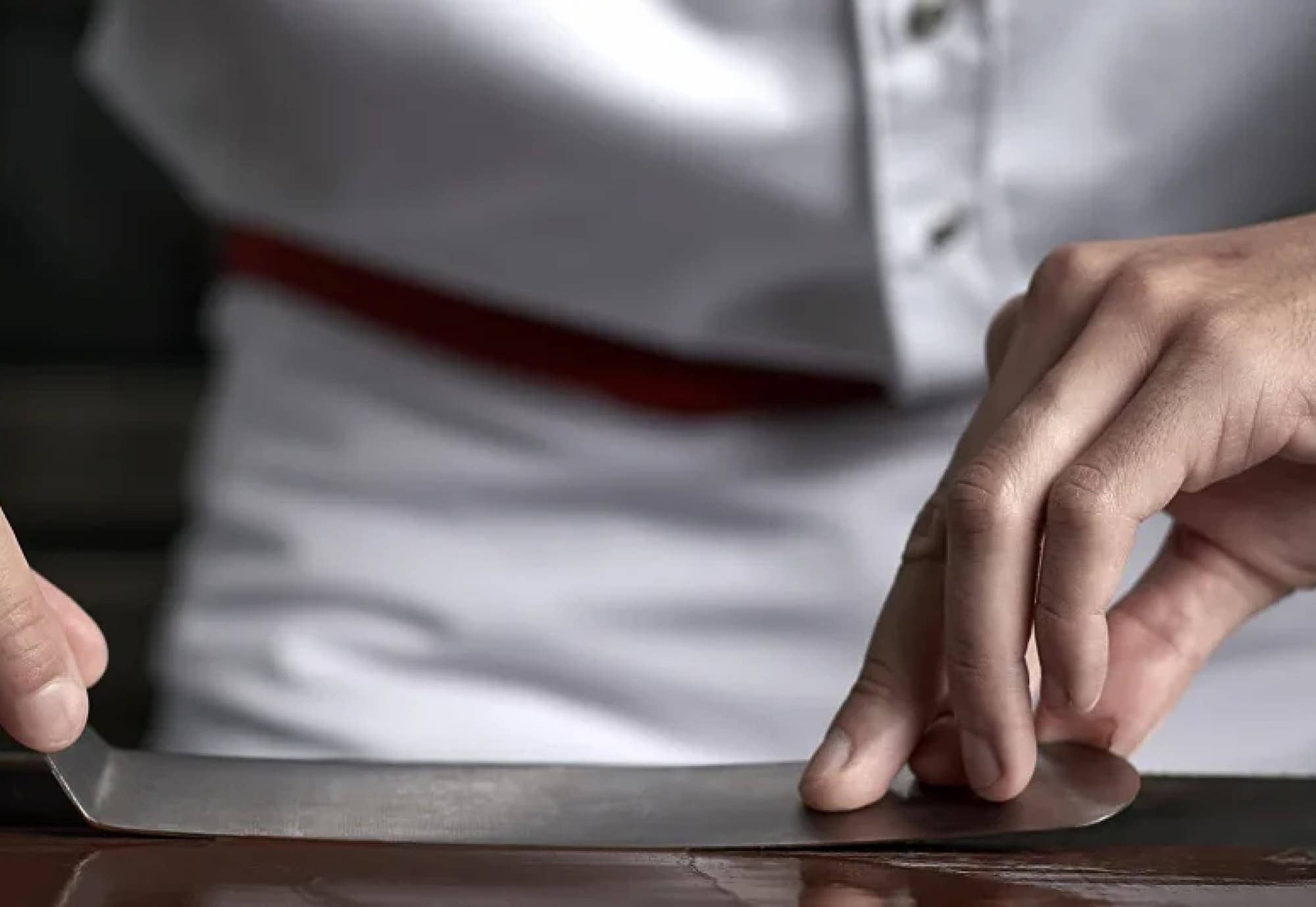
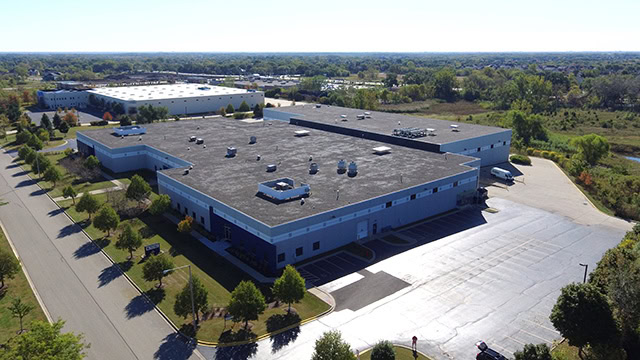
Why manufacturers choose Mercateam
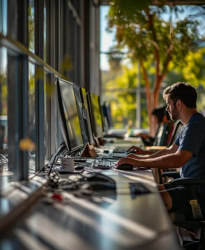
Your secure data
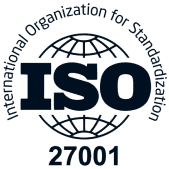
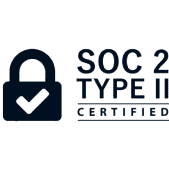
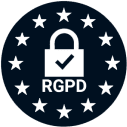
Take back control of your production teams' skills
and organization now.
Book a demo