A Major Challenge for Competitiveness
The manufacturing sector is currently going through a profound know-how crisis that directly threatens its competitiveness. This situation is characterized by a gradual but steady erosion of essential technical skills within companies. When a plant can no longer master the techniques specific to its production, it exposes itself to increasing quality defects and significant delivery delays.
These operational difficulties have a direct impact on customer satisfaction and, consequently, on a company's market share. Production delays and quality defects not only lead to additional costs, but also to a loss of confidence on the part of customers, which can lead to a lasting deterioration in the company's competitive position.
The proliferation of non-conformities and production errors often reveals a loss of control over complex industrial processes. This situation is all the more worrying given the ever-increasing demands for quality and precision in modern industry.
Structural causes of the manufacturing crisis
This skills crisis is rooted in a number of structural phenomena that are profoundly affecting the manufacturing sector. The aging of the workforce is one of the major challenges. Many companies are facing a major wave of retirements of technical experts who take with them decades of experience and know-how.
Passing on knowledge from one generation to the next is particularly complex, not least because of differences in professional culture and working methods. The older generations, with their expertise acquired in the field, sometimes find it difficult to formalize and pass on their knowledge to new arrivals.
At the same time, the manufacturing sector is undergoing rapid technological transformation, with the arrival of new machines, automated processes and innovative production methods. This evolution requires constant adaptation of skills, creating a gap between traditional know-how and the new demands of the sector.
Finally, the manufacturing sector suffers from a lack of attractiveness to young talent. The traditional image of industry, often perceived as lacking in innovation and reward, is holding back the recruitment of new generations of skilled professionals. This situation creates a vicious circle in which the lack of renewal of the workforce accentuates the loss of skills.
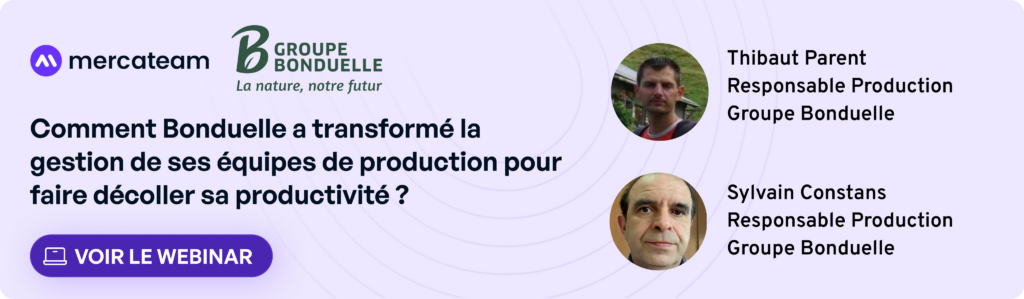
Strategic challenges facing the manufacturing sector
Preserving Critical Skills
The preservation of critical skills represents a fundamental challenge for the manufacturing sector. First and foremost, companies need to identify the know-how that is essential to their business. This involves an in-depth analysis of production processes and the technical expertise essential to their smooth operation.
Visit expertise mapping is a crucial step in this process. It enables us to identify areas of vulnerability, in particular skills held by a limited number of employees, or those threatened by upcoming retirements. This visibility makes it possible to anticipate the necessary knowledge transfers and assess the potential impact on production in the event of the loss of these skills.
Anticipating future skills needs requires a forward-looking vision of the sector. Companies must not only maintain their current know-how, but also develop the skills that will be needed tomorrow, taking into account technological developments and market changes.
Operational Performance
Maintaining production quality remains an absolute priority. In a highly competitive environment, mastery of manufacturing processes and product compliance with quality standards are essential to maintain customer confidence.
Optimizing industrial processes requires continuous improvement in work methods. This optimization must take into account both technical and human aspects, ensuring team efficiency while preserving critical know-how.
Visit managing versatility is becoming a major strategic lever. Not only does it make it possible to cope with the vagaries of production, it also enriches the skills of employees, contributing to their motivation and professional development.
Solutions and Areas for Improvement
Training and Knowledge Transfer
Structured mentoring programs are an effective response to the challenge of knowledge transfer. These programs enable experts to share their experience with new employees in a formalized, long-term framework. The development of personalized training paths complements this approach, by adapting the content and pace of learning to the specific needs of each employee.
Modernization of management tools
The digitization of skills matrices represents a major step forward in talent management. It enables real-time monitoring of available skills and facilitates the identification of training needs. The automation of training follow-up and the introduction of continuous assessment systems enable more dynamic, reactive management of skills development.
Attracting and retaining talent
Developing attractive career paths is becoming crucial to attracting and retaining talent. These paths must offer clear and rewarding prospects for advancement, supported by skills recognition systems that value technical expertise.
Partnerships with educational establishments help to create talent pools and train future employees in the sector's specific features. These partnerships can take the form of work-study programs, internships or joint R&D projects.
Improving working conditions and the working environment also plays a decisive role in the attractiveness of the sector. Particular attention needs to be paid to modernizing workspaces, workstation ergonomics and quality of life at work.
Innovation in Skills Management
The digital transformation of the manufacturing sector today calls for a profound overhaul of business methods. skills management. The adoption of modern collaborative tools enables teams to share knowledge and experience more fluidly and efficiently. These platforms facilitate exchanges between experts and learners, creating an environment conducive to the transfer of know-how.
Visit digital training platforms are revolutionizing corporate learning. They offer unprecedented flexibility in accessing training content, and enable personalized monitoring of each learner's progress. These solutions make it possible to create learning paths tailored to the specific needs of each employee, while ensuring complete traceability of the training received.
The development of knowledge management systems is a major step forward. These systems capitalize on the company's collective expertise by documenting best practices, critical procedures and feedback. Artificial intelligence enhances these systems by optimizing learning processes and facilitating the identification of critical skills to be developed.
Change Management
The success of this digital transformation depends largely on the quality of change management. Training managers in the new digital tools is essential. Not only must they master these tools, but they must also understand their potential, so as to better support their teams in this transition.
Raising team awareness of the challenges of transformation is an essential pillar of change. It is crucial to make every employee understand the importance of this evolution and the benefits it brings, both for the company and for their personal development.
Solid technical and methodological support must be put in place to accompany this transformation. This support enables any difficulties encountered to be resolved quickly, and ensures optimum adoption of the new digital solutions. Regular communication on progress and successes boosts team motivation and maintains the momentum for change.
Conclusion
The skills crisis in the manufacturing sector represents a major challenge requiring a global, coordinated approach. Its resolution requires a profound transformation of practices, combining technological innovation and human development. This transformation can only succeed if it is supported by a clear vision shared by all company players.
Investment in training is a fundamental pillar of this transformation. It must go hand in hand with the modernization of management tools and a thorough review of the sector's attractiveness. These combined efforts will enable us to build a more resilient, high-performance manufacturing sector, capable of meeting current and future challenges.
The success of this transformation depends on a subtle balance between technological innovation and the human dimension. Companies that know how to strike this balance will be best equipped to maintain their competitiveness and ensure their long-term survival in a constantly changing environment. The future of the manufacturing sector thus lies in its ability to embrace change while preserving and developing its precious know-how.