Industry 4.0 is redefining production methods and the place of employees within factories. More than just a technological revolution, it represents a profound transformation that places people at the heart of industrial issues.
Understanding Industry 4.0
A new approach to industrial production
The concept of Industry 4.0 refers to the integration of digital technologies into manufacturing processes to create connected, intelligent factories. The aim? To make production more flexible and efficient, while enhancing the value of our teams' know-how.
This approach breaks with the traditional vision of automation, which was primarily aimed at replacing humans. Instead, Industry 4.0 seeks to enhance operators' capabilities by equipping them with intelligent tools.
The four industrial revolutions
Industrial history has undergone four major transformations:
- 1780: Mechanization with the arrival of the steam engine
- 1870: Electrification and mass production
- 1970: Automation with electronics and computers
- 2011: Digitization with connected technologies
Performance-enhancing technologies
Six technological pillars structure Industry 4.0:
- The Internet of Industrial Things (IoT): connected sensors provide real-time production data
- Artificial intelligence: algorithms that analyze data to optimize processes
- The cloud: an infrastructure that centralizes and shares information
- Digital twins: virtual replicas of equipment for simulation and anticipation
- Augmented reality: tools to assist operators in their tasks
- Cybersecurity: protocols that protect systems and data
Concrete impacts on your production site
Optimized, more flexible production
Visit digitalization allows production lines to be quickly adapted to customer requirements. Operators have access to clear overview of production orders and can adjust parameters in real time. The result: less waste and better quality.
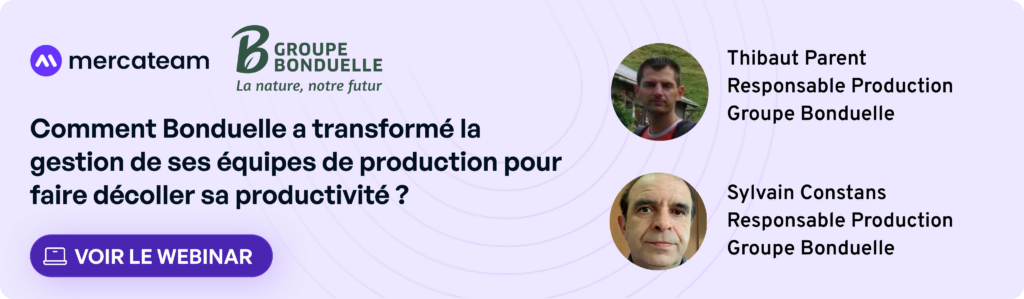
Predictive maintenance as a performance driver
IoT sensors detect early warning signs of breakdowns. This enables maintenance teams to intervene at the right time and avoid unplanned downtime. This predictive approach reduces costs and improves equipment availability.
More qualified and autonomous teams
Industry 4.0 brings with it the need to employee skills development. Operators are developing new areas of expertise, particularly in data analysis and the use of digital tools. They gain autonomy and can make informed decisions.
Redesigned man-machine collaboration
Collaborative robots (cobots) work alongside operators to assist them with tedious or repetitive tasks. Man-machine interfaces become more intuitive. This complementarity enables teams to concentrate on high value-added activities.
Industry 4.0 is not just about technology. It is profoundly transforming the organization of work and the role of employees. The key to success? Accompany this transformation by putting people at the heart of our concerns.
Benefits for your employees
New career prospects
Industry 4.0 is transforming traditional professions and creating new opportunities. Operators are becoming skilled technicians capable of interacting with intelligent production systems. Team leaders are evolving into coordinators, analyzing data to optimize the performance of their lines.
Career paths are taking shape: an operator can specialize in predictive maintenance or connected quality. Visit skills acquired open doors to positions of greater responsibility.
A redesigned work environment
Digitization considerably reduces the physical workload on operators:
- Cobots take on repetitive tasks
- Tablets replace paper documents
- Connected equipment alerts you to anomalies
- Augmented reality guides technical gestures
These improvements reduce drudgery and the risk of accidents. Teams can concentrate on more rewarding tasks.
Continuous skills upgrading
Employees benefit from training adapted to the evolution of their business with Industry 4.0:
- Use of digital tools
- Production data analysis
- First-level maintenance
- Solving complex problems
These new skills enhance their expertise and strengthen their employability. Visit training becomes more interactive with digital media and real-life situations.
More autonomy at work
Operators now have the tools to :
- Track their performance indicators
- Making data-driven decisions
- Suggest improvements
- Share their expertise
This increased autonomy strengthens their commitment and their feeling of contributing to the company's performance.
Transformation challenges
Supporting cultural change
Digital transformation is revolutionizing the way we work. To succeed, it requires :
- A clear vision shared by all
- Involved local management
- Transparent communication on objectives
- Quick wins to demonstrate benefits
Human support remains the key to success, beyond the technological aspects.
Developing skills
Adapting skills is a major challenge:
- Identifying future needs
- Designing appropriate training paths
- Recruiting new profiles
- Transfer of existing know-how
A skills development plan to anticipate and prepare for these changes.
Safety as a priority
Cybersecurity is becoming a strategic issue:
- Production data protection
- Securing connected equipment
- Training teams in best practices
- Regulatory compliance (RGPD)
Employee confidence also depends on guaranteeing the protection of their data.
A business model to be defined
Investment in Industry 4.0 must be based on a solid business case:
- Measurable productivity gains
- Reduced maintenance costs
- Quality improvement
- Greater flexibility
Return on investment also includes less tangible benefits such as team commitment and company attractiveness.
Transformation 4.0 is not just a question of technology. Its success depends above all on the ability to mobilize teams and leverage their skills in this new industrial context.
Methodology: successfully making the transition to Industry 4.0
A step-by-step transformation
To succeed in your 4.0 transformation, you need a gradual, structured approach:
- Initial diagnosis
- Inventory of existing processes
- Digital maturity assessment
- Identifying field irritants
- Skills mapping
- Strategy definition
- Prioritizing high-impact projects
- Choosing the right technologies
- Building the roadmap
- Defining success indicators
- Selection of a test line or workshop
- Training pilot teams
- Measuring initial results
- Adjustments before global deployment
Key success factors
Our experience with over 300 industrial sites shows that success depends on :
- Involving local management from the outset
- Ongoing training of teams in new tools
- Setting up a multidisciplinary project team
- Sustained support in the field
- Making the most of early successes
Eloquent feedback
Let's take the example of LVMH Fragrance Brands which has digitized its Beauvais site:
- 40% reduction in integration time for new arrivals
- Gain of a quarter FTE on planning
- Competency matrices updated quarterly
- Better response to absences
Or Unither Pharmaceuticals who obtained :
- 50% to reduce Excel planning files
- Real-time schedule updates visible in the workshop
- Optimized cost monitoring
- Better territoriality of skills
Helping teams succeed
Human support is structured around 4 axes:
- Communication
- Regular sharing of progress
- Listening to feedback from the field
- Celebrating success
- Quick resolution of problems
- Sessions tailored to your needs
- Interactive digital media
- Peer training
- Learning assessment
2. Field support
- Regular presence in the field
- Fast problem solving
- User coaching
- Accessible documentation
- Identifying ambassadors
- Sharing best practices
- Community animation
- Continuous performance measurement
Industry 4.0 prospects and developments
Trends shaping the industry
New opportunities are emerging:
- Generative artificial intelligence to optimize production
- Digital twins for process simulation
- The circular economy for a more sustainable industry
- Mass customization thanks to flexible lines
The industry of tomorrow takes shape
Industrial work is evolving towards :
- More man-machine collaboration
- Data-driven decision-making
- Flexible, customized production
- A controlled environmental impact
Industrial sites are becoming places of innovation, where operators use cutting-edge technologies to produce better, faster and more responsibly.
The trades of tomorrow take shape
New roles are emerging in the industry:
- Expert in industrial data analysis
- Predictive Maintenance Technician
- Human-robot coordinator
- Specialist in digital operational excellence
These professions combine technical expertise and digital skills, opening up new prospects for employees.
Industry 4.0 represents a unique opportunity to reinvent production while valuing people. The companies that succeed in their transformation will be those that place their employees at the heart of this evolution.