L’industrie 4.0 redéfinit les modes de production et la place des collaborateurs au sein des usines. Plus qu’une simple révolution technologique, elle représente une transformation profonde qui place l’humain au cœur des enjeux industriels.
Comprendre l’industrie 4.0
Une nouvelle approche de la production industrielle
Le concept d’industrie 4.0 désigne l’intégration des technologies numériques dans les processus de fabrication pour créer des usines connectées et intelligentes. L’objectif ? Rendre la production plus flexible, plus efficace tout en valorisant le savoir-faire des équipes.
Cette approche rompt avec la vision traditionnelle de l’automatisation qui visait principalement à remplacer l’humain. L’industrie 4.0 cherche au contraire à augmenter les capacités des opérateurs en les dotant d’outils intelligents.
Les quatre révolutions industrielles
L’histoire industrielle a connu quatre grandes transformations :
- 1780 : La mécanisation avec l’arrivée de la machine à vapeur
- 1870 : L’électrification et la production de masse
- 1970 : L’automatisation avec l’électronique et l’informatique
- 2011 : La digitalisation avec les technologies connectées
Les technologies au service de la performance
Six piliers technologiques structurent l’industrie 4.0 :
- L’Internet des Objets Industriels (IoT) : des capteurs connectés qui remontent les données de production en temps réel
- L’intelligence artificielle : des algorithmes qui analysent ces données pour optimiser les process
- Le cloud : une infrastructure qui centralise et partage l’information
- Les jumeaux numériques : des répliques virtuelles des équipements pour simuler et anticiper
- La réalité augmentée : des outils qui assistent les opérateurs dans leurs tâches
- La cybersécurité : des protocoles qui protègent les systèmes et les données
Les impacts concrets sur votre site de production
Une production optimisée et plus flexible
La digitalisation permet d’adapter rapidement les lignes de production aux besoins des clients. Les opérateurs disposent d’une vision claire des ordres de fabrication et peuvent ajuster les paramètres en temps réel. Résultat : moins de gaspillage et une meilleure qualité.
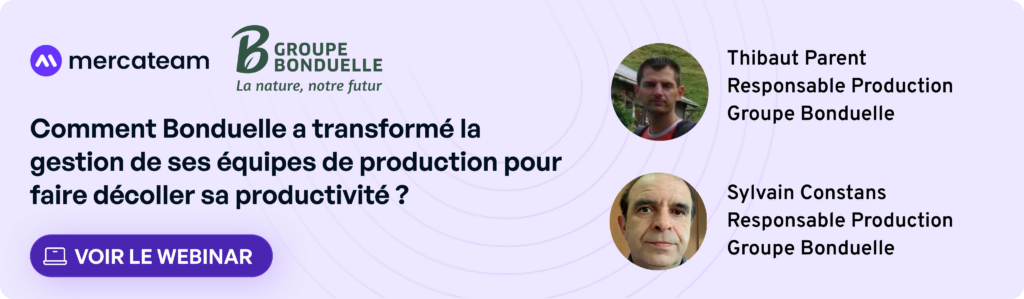
La maintenance prédictive comme levier de performance
Les capteurs IoT détectent les signes avant-coureurs de pannes. Les équipes de maintenance peuvent ainsi intervenir au bon moment et éviter les arrêts non planifiés. Cette approche prédictive réduit les coûts et améliore la disponibilité des équipements.
Des équipes plus qualifiées et autonomes
L’industrie 4.0 s’accompagne d’une montée en compétences des collaborateurs. Les opérateurs développent de nouvelles expertises, notamment dans l’analyse des données et l’utilisation des outils digitaux. Ils gagnent en autonomie et peuvent prendre des décisions éclairées.
Une collaboration homme-machine repensée
Les robots collaboratifs (cobots) travaillent aux côtés des opérateurs pour les assister dans les tâches pénibles ou répétitives. Les interfaces homme-machine deviennent plus intuitives. Cette complémentarité permet aux équipes de se concentrer sur les activités à forte valeur ajoutée.
L’industrie 4.0 ne se résume pas à la technologie. Elle transforme en profondeur l’organisation du travail et le rôle des collaborateurs. La clé du succès ? Accompagner cette transformation en plaçant l’humain au centre des préoccupations.
Les bénéfices pour vos collaborateurs
De nouvelles perspectives professionnelles
L’industrie 4.0 transforme les métiers traditionnels et crée de nouvelles opportunités. Les opérateurs deviennent des techniciens qualifiés capables d’interagir avec des systèmes de production intelligents. Les chefs d’équipe évoluent vers un rôle de coordinateur, analysant les données pour optimiser les performances de leurs lignes.
Des parcours d’évolution se dessinent : un opérateur peut se spécialiser en maintenance prédictive ou en qualité connectée. Les compétences acquises ouvrent des portes vers des postes à responsabilité accrue.
Un environnement de travail repensé
La digitalisation allège considérablement la charge physique des opérateurs :
- Les cobots prennent en charge les tâches répétitives
- Les tablettes remplacent les documents papier
- Les équipements connectés alertent en cas d’anomalie
- La réalité augmentée guide les gestes techniques
Ces améliorations réduisent la pénibilité et les risques d’accident. Les équipes peuvent se concentrer sur des missions plus enrichissantes.
Une montée en compétences continue
Les collaborateurs bénéficient de formations adaptées à l’évolution de leur métier avec l’industrie 4.0 :
- Utilisation des outils digitaux
- Analyse des données de production
- Maintenance de premier niveau
- Résolution de problèmes complexes
Ces nouvelles compétences valorisent leur expertise et renforcent leur employabilité. La formation devient plus interactive avec des supports digitaux et des mises en situation.
Plus d’autonomie dans le travail
Les opérateurs disposent désormais d’outils pour :
- Suivre leurs indicateurs de performance
- Prendre des décisions basées sur les données
- Proposer des améliorations
- Partager leur expertise
Cette autonomie accrue renforce leur engagement et leur sentiment de contribuer à la performance de l’entreprise.
Les enjeux de la transformation
Un changement culturel à accompagner
La transformation digitale bouleverse les habitudes de travail. Pour réussir, elle nécessite :
- Une vision claire partagée par tous
- Un management de proximité impliqué
- Une communication transparente sur les objectifs
- Des quick wins pour démontrer les bénéfices
L’accompagnement humain reste la clé du succès, au-delà des aspects technologiques.
Des compétences à faire évoluer
L’adaptation des compétences représente un défi majeur :
- Identification des besoins futurs
- Conception de parcours de formation adaptés
- Recrutement de nouveaux profils
- Transfert des savoir-faire existants
Un plan de développement des compétences structuré permet d’anticiper et de préparer ces évolutions.
La sécurité comme priorité
La cybersécurité devient un enjeu stratégique :
- Protection des données de production
- Sécurisation des équipements connectés
- Formation des équipes aux bonnes pratiques
- Conformité réglementaire (RGPD)
La confiance des collaborateurs passe aussi par la garantie de la protection de leurs données.
Un modèle économique à définir
L’investissement dans l’industrie 4.0 doit s’appuyer sur un business case solide :
- Gains de productivité mesurables
- Réduction des coûts de maintenance
- Amélioration de la qualité
- Flexibilité accrue
Le retour sur investissement intègre aussi des bénéfices moins tangibles comme l’engagement des équipes et l’attractivité de l’entreprise.
La transformation 4.0 n’est pas qu’une question de technologie. Son succès repose avant tout sur la capacité à mobiliser les équipes et à valoriser leurs compétences dans ce nouveau contexte industriel.
Méthodologie : réussir le passage à l’industrie 4.0
Une transformation par étapes
Pour réussir votre transformation 4.0, une approche progressive et structurée s’impose :
- Diagnostic initial
- État des lieux des processus existants
- Évaluation de la maturité digitale
- Identification des irritants terrain
- Cartographie des compétences
- Définition de la stratégie
- Priorisation des chantiers à fort impact
- Choix des technologies adaptées
- Construction de la feuille de route
- Définition des indicateurs de succès
- Sélection d’une ligne ou d’un atelier test
- Formation des équipes pilotes
- Mesure des premiers résultats
- Ajustements avant déploiement global
Les facteurs clés du succès
Notre expérience avec plus de 300 sites industriels montre que la réussite repose sur :
- L’implication du management de proximité dès le départ
- La formation continue des équipes aux nouveaux outils
- La mise en place d’une équipe projet pluridisciplinaire
- Un accompagnement terrain soutenu
- La valorisation des premiers succès
Des retours d’expérience éloquents
Prenons l’exemple de LVMH Fragrance Brands qui a digitalisé son site de Beauvais :
- Réduction de 40% du temps d’intégration des nouveaux arrivants
- Gain d’un quart d’ETP sur la planification
- Matrices de compétences mises à jour chaque trimestre
- Meilleure réactivité face aux absences
Ou encore Unither Pharmaceuticals qui a obtenu :
- 50% de réduction des fichiers Excel de planification
- Mise à jour en temps réel du planning visible en atelier
- Optimisation du suivi des coûts
- Meilleure territorialité des compétences
Accompagner les équipes vers le succès
L’accompagnement humain se structure autour de 4 axes :
- Communication
- Partage régulier des avancées
- Écoute des retours terrain
- Célébration des succès
- Traitement rapide des difficultés
- Sessions adaptées aux besoins
- Supports digitaux interactifs
- Formation par les pairs
- Évaluation des acquis
2. Support terrain
- Présence régulière sur le terrain
- Résolution rapide des problèmes
- Coaching des utilisateurs
- Documentation accessible
- Identification des ambassadeurs
- Partage des bonnes pratiques
- Animation de la communauté
- Mesure continue des résultats
Perspectives et évolutions de l’industrie 4.0
Les tendances qui façonnent l’industrie
De nouvelles opportunités émergent :
- L’intelligence artificielle générative pour optimiser la production
- Les jumeaux numériques pour simuler les process
- L’économie circulaire pour une industrie plus durable
- La personnalisation de masse grâce à la flexibilité des lignes
L’industrie de demain se dessine
Le travail industriel évolue vers :
- Plus de collaboration homme-machine
- Des prises de décision basées sur les données
- Une production flexible et personnalisée
- Un impact environnemental maîtrisé
Les sites industriels deviennent des lieux d’innovation où les opérateurs utilisent des technologies de pointe pour produire mieux, plus vite et de manière plus responsable.
Les métiers de demain prennent forme
De nouveaux rôles apparaissent dans l’industrie :
- Expert en analyse de données industrielles
- Technicien en maintenance prédictive
- Coordinateur homme-robot
- Spécialiste en excellence opérationnelle digitale
Ces métiers combinent expertise technique et compétences digitales, ouvrant de nouvelles perspectives aux collaborateurs.
L’industrie 4.0 représente une opportunité unique de réinventer la production tout en valorisant l’humain. Les entreprises qui réussiront leur transformation seront celles qui auront su placer leurs collaborateurs au cœur de cette évolution.